The benefits of measuring OEE in real-time
Blog

Overall Equipment Effectiveness (OEE) measures the six big causes of lost production, providing organizations with an overall measure of asset utilization.
The term was created by Seiichi Nakajima, the founder of the Total Productive Maintenance system, and is based on the Harrington Emerson way of thinking regarding labor efficiency, to provides you with a single score for your manufacturing performance.
As a measure, it’s useful for manufacturers in lots of ways, primarily however, it provides manufacturers with a way to compare and contrast its performance in numerous ways, (such as line x line, between products, facilities or regions) to see how effective they’re being vs. the maximum potential output of their manufacturing process.
The difficulties of measuring OEE and why IoT fixes that
Measuring OEE is difficult because there’s lots of moving parts, machines aren’t necessarily networked, comms are limited, technology hasn’t historically been up to scratch.
What this has led to is lag measures of OEE, sometimes still done manually, based on a snapshot of performance after the fact – meaning that by the time you know what your score is, it’s too late to do anything about. Not only that, without transparency into the individual inputs that are going in to make that score over long periods of time, it can be incredibly difficult to spot trends hidden in the data that could be invaluable to the business.
IoT changes this. Not only can you retrofit old machinery and technologies to collect data about their performance – reducing the need for expensive capital-intensive investment – but the flexibility of some manufacturing Industry 4.0 solutions means that you don’t need to change how you’re currently operating to incorporate it (or until you have the data at hand to do it to make improvements).
Additionally, the ability to connect and unite data sources from previously disparate systems into a single solution not only enables you to utilize Data Science to get to the bottom of what our OEE is at any given moment, but provides you with a window to look at historical and, with work, future performance based on your current set-up.
The 11 benefits of measuring OEE in real-time
Knowing real-time OEE has important effects beyond just having the information to hand at any given time.
Measuring OEE in real-time has numerous obvious and hidden benefits, enabling you to:
- Establish an accurate baseline OEE calculation – with accurate monitoring of all of your inputs consistently, accurately and over a prolonged period of time, you can establish an accurate baseline OEE calculation, rather than just a snapshot one. From it, you can then identify what under and over performance actually looks like and trigger alerts set at custom thresholds that cause action (whether manual or automated) to be taken.
- Get the ability to make real-time production improvements – your production team can see how they’re performing against their daily targets, where the problems lie, and make make immediate Improvements. Learn where to focus your scarce improvement resources through OEE and help you to identify where and when rate losses, stoppages and yield losses most affect your production.
- Better prioritize future optimizations – managers can analyze their holistic line performance to tweak processes and inputs to plan for future optimizations.
- Better establish the ROI of OEE’s inputs – whether machinery, human capital or something else, you can play with the unique mix of things that goes into your operations and see instantly the effect that it’s having and establish the ROI on any investment.
- Take a step towards predictive maintenance – understanding your OEE in real-time will enable you to see the performance of each part of your manufacturing chain. From this, it may be possible to identify machinery that’s underperforming over time, whether it’s going slow or causing minor stoppages. From that, you can better identify maintenance requirements and fix issues before they become catastrophic failures.
- Discover the ‘Hidden Factory’ – there are lots of things that go intro production output that aren’t always transparent, such as unwritten processes or manual inputs. With putting in place real-time OEE measurements, you’ll be able to root these out and design better operation models to improve performance.
- Improve energy efficiency – machine energy consumption depends on the product processed and machine efficiency: an inefficient machine can consume as much as a productive one. Uncover the hidden cost of inefficient energy consumption.
- Enhance yield – stops, start ups and setup adjustments all reduce yield and produce scrap. Identify the sources of yield losses through overall equipment effectiveness.
- Track production in real-time – enables factory managers to monitor actual production and profitability compared to the set targets in real-time, so that they can take action if performance is below expectations.
- Reduce downtime – understand where and when downtime occurs so that you can be proactive about uptime and utilize the information to inform your equipment modification, staff and maintenance schedules.
- Empower your workforce – by your people the data and power to make changes in real-time, you are providing them with the insights needed to make positive changes for your business. Not only is this good for overall numbers, but evidence shows that it can also increase job satisfaction.
Is this all the benefits of measuring OEE in real-time?
No. People are already talking about Industry 5.0 and having a fully-automated, self-healing factory that requires minimal human intervention when we’ve not really got to 4.0 (truly) yet. However, to be ready for the automated, self-healing, human-less factories of the future; then the above steps are the beginning of that (long) journey.
Factory One enables you to solve many manufacturing problems and achieve strategic objectives out-of-the-box using our ready-to-deploy modules - speak to us to find out more.
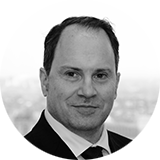
Dr Bernard Kornfeld
Chief Scientist
LinkedIn
Get started with your own transformation today, fast and affordably.
Factory One's easy-to-use solution, complete with ready-to-deploy modules that can improve every aspect of your manufacturing operations, will give you all the abilities you need, plus much more, in weeks with no hidden-costs.
Speak to us today to get started.