The difference between Reactive, Preventative, Condition-based and Predictive Maintenance
Blog

There are numerous different maintenance strategies, but what are they all? Where are they best applied in an industrial or business context? And what are the benefits of them? Let’s take a closer look and find out…
Reactive Maintenance
What it is: it’s a form of unplanned maintenance and is simply when you fix something after it breaks.
Example: replacing a light bulb. You replace a light bulb once it has blown.
Weaknesses: because it only addresses the problem once its occurred, if used in the wrong place, it could be disruptive to wider operations or lead to catastrophic failures which are dangerous to staff, shorten the lifespan of machinery and cause very expensive and time consuming fixes.
Strengths: low upfront and ongoing costs, doesn’t require any planning and needs no capital investment.
When is it often used: You see it typically applied for assets that are of low value, that don’t have a major impact on your operations, are easy to replace, and are, because of it, highly-disposable – i.e. the cost of predicting failure would far outweigh the benefit. Sure, you could spend a fortune monitoring the temperature of the bulb, detecting energy usage irregularities, or that its output has gone down by a few lumens, but what’s the point if the lightbulb is one of a dozen in a corridor in your office building.
Preventative Maintenance
What it is: it’s when you attempt to prevent the failure of an asset or machinery by doing regular maintenance at predetermined intervals during its lifecycle.
Example: HVAC servicing. You may give your industrial air conditioning units a service and check-over once or twice a year depending on usage.
Weaknesses: requires diligent planning and record keeping, to have ready-access to maintenance crews (so expensive), and can lead to unnecessary services, part replacement, downtime and asset underutilization.
Strengths: requires limited upfront costs, but reduces downtime and requires no upfront capital investments.
When is it often used: when the cost to maintain the asset is moderate and it going offline is only an inconvenience, that there are windows in its usage schedule that mean it can be done without taking it offline for long periods, and that failure will have an impact on a small part of the operation rather than bringing everything to stop.
Condition-based Maintenance
What it is: like preventive maintenance, but considers how an asset has been and is being used to determine when servicing should occur. In some instances, this will be directed by the asset themselves if they have internal systems that can detect faults.
Example: fleet servicing. You service your trucks every 10,000kms, every 4,000 hours of usage, or when you get a warning light on the dashboard of your vehicle.
Weaknesses: limited accuracy when it comes to predicting a failure, may still lead to unnecessary downtime and service costs.
Strengths: maintenance occurs when it’s much more likely to be needed and, in some instances, is based off of real-time data or insights, meaning that faults are known and quicker to fix. This will extend the lifespan of the asset, improve utilization, and reduce the risks of catastrophic failure and downtime.
When should it be used: when the maintenance costs aren’t particularly high and you can schedule asset downtime to fit with your operations schedule. Many modern ‘smart’ assets and technologies come with condition-based maintenance functionality built into it, but it’s also possible to roll out retrospectively by applying IoT sensors and meters to existing machinery to detect faults – but don’t confuse it with Predictive Maintenance just because you’re using IoT technologies!
Predictive Maintenance
What it is: Predictive Maintenance relies on the close monitoring of assets using IoT technologies (such as meters and sensors), Data Science and Machine Learning to predict when machinery needs to be serviced. It does this by feeding this information into an IoT platform and then relying on the system to find trends in the data coming into it (from multiple sources and comparing it to historical data) to predict failure and inform maintenance crews of required work.
Example: on a manufacturing line. You monitor the productivity, energy usage, temperature, speed, vibrations, hours of continuous use, etc. to detect anomalies that are impossible for humans to spot that indicate a forthcoming failure.
Weaknesses: needs expert IoT, Data Science and Machine Learning knowledge to implement; requires upfront capital investment; and requires time to finetune to predict every type of failure.
Strengths: can schedule maintenance to occur during scheduled downtimes, reduces time to fix, increases asset lifespan, reduces downtime, increases asset utilization, improves safety, and enables efficiency savings (e.g. energy usage).
When should it be used: when the failure of an asset (even minor) causes major disruption to a businesses operation, when maintenance and parts costs are high, there are many variables that go into predicting the failure of the machinery, or when a problem can cause a major health and safety risk.
Much like many business problems not being IoT ones, not all of your assets and machinery need Predictive Maintenance – it’s not always economically viable or desirable. However, for business-critical assets that you need to have minimal downtime, it’s by far and away the most efficient and cost-effective way to maintain those assets.
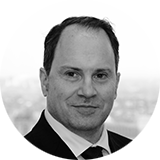
Dr Bernard Kornfeld
Chief Scientist
LinkedIn
Get started with your own transformation today, fast and affordably.
Factory One's easy-to-use solution, complete with ready-to-deploy modules that can improve every aspect of your manufacturing operations, will give you all the abilities you need, plus much more, in weeks with no hidden-costs.
Speak to us today to get started.