Greenhouse Management, Monitoring & Yield
Case Study

Using Factory One to improve greenhouse management, monitoring and yields.
The problem.
The rapid growth in demand for newer, non-traditional crops, as well as ongoing demand for fresh fruit and vegetables year-round – no matter the season - has created fresh opportunities for greenhouse farming.
With this opportunity also comes the need for closer scrutiny on delivery, costs and product quality. This is forcing farmers to improve their operational efficiency and overall greenhouse management practices, with Industry 4.0 solutions the ideal fit to help them to do just that.
The solution.
Farmers need to monitor all of the environmental characteristics of their greenhouses that have an effect on crop yield and timing, and to optimize those factors in order to maximize yield, so it’s critical for the solution to ensure that the right technologies and processes are put in place to capture accurate information in real-time.
Better manage your greenhouses through monitoring to deliver yield optimization.
Defining what data to collect is critical
In order to create the solution so that the information can be acted upon to deliver the required yield optimization, we started by identifying the key data required. In this solution, this included:
- Room temperature
- Humidity
- CO₂ levels
- Soil temperature and moisture
- Lights status (on/off)
- Nutrient injection volume and timing
- Water flow rates
Initial goals of the solution
The first goal of building the solution was to connect the Dynamix platform with the proprietary greenhouse SCADA so that data would be collected consistently and reliably, ensuring data quality and integrity. This would then provide the following outcomes:
- The ability to monitor real-time data received from the SCADA via a web-based and mobile system
- Ensure device management of the SCADA was set in place
- Define business logic to the application in-order to meet the greenhouse growers business objectives
- Provide alarm and alert notifications via email or SMS messages when there was communication downtime
- Start collecting enough historical data to enable the ability to test different logic to predict yield
- Providing real-time SMS notification when environmental thresholds aren’t not met and there is risk for for reduced yield
- Test the application, making sure all of the above goals are met, based on the below solution architecture.
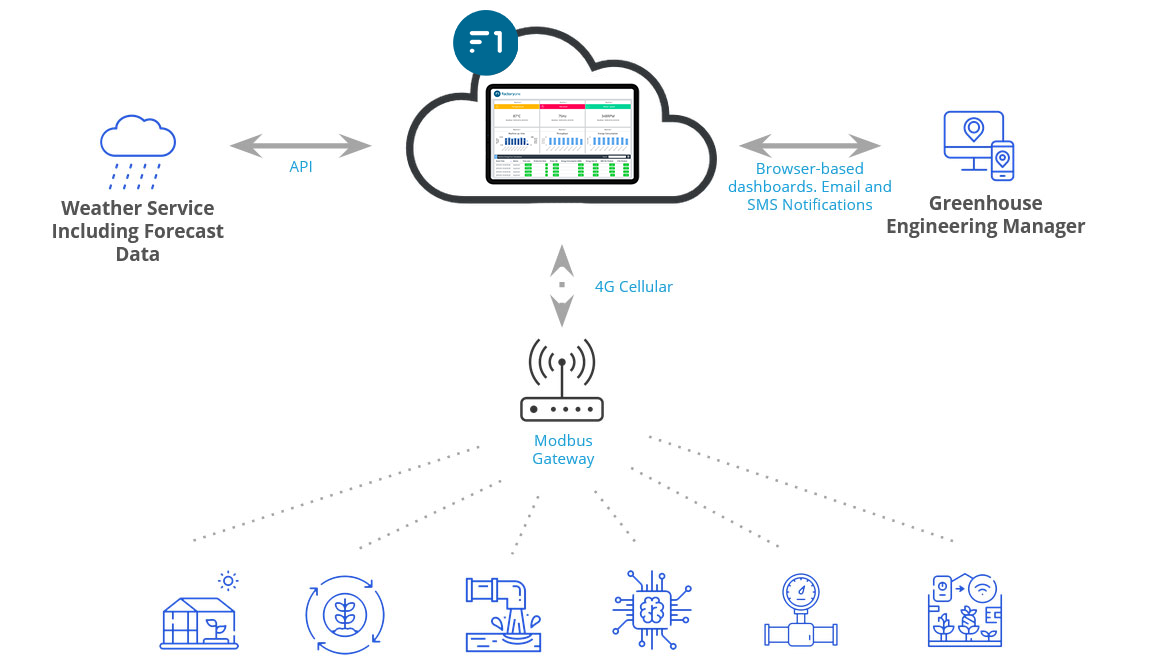
Testing.
Before setting the solution live, we tested four critical aspects of the solution:
1) Security
The solution is built with security as a top priority and our proprietary security architecture ensures that data is secure at all points of the environment.
The solution includes data encryption in transit from device-to-cloud, as well as device authentication; security (Bearer) tokens; SSL, AES and RSA encryption; as well as additional device security checks done via automated polling.
2) Connectivity
In order to retrieve the data, we integrated MODBUS to the greenhouse advanced control hardware management system, enabling us to retrieve over 100 data points every 30 seconds from the control hardware management system. In addition we connected to additional sensors in the greenhouse which weren’t controlled via the control hardware management system, like door sensors. All of this information is then sent directly to the Rayven cloud IoT platform.
3) Data integrity
Once data started flowing from the control hardware management system and the sensors, the first task was to translate some of the MODBUS tag codes into a readable format, which meant creating custom logic translators to the code. Then, we also created sophisticated case logic in the Rayven codeless work flow to visualize the large variety of translated data and validate it against what was being seen on the local greenhouse system in real-time.
4) Industrial data science
The objective of exploratory data analysis was to observe trends in the data and provide insights into what environmental factors may effect optimized yield:
- Create an algorithm that defines optimal growth patterns
- Create alerts when specific environmental settings are effecting yield
- Compare greenhouse rooms to identify parameters that may effect yield
- Forecast yield based on current environmental settings.
What’s next?
We are continuing to collect and visualize the insights that are coming through and continuing improve our forecasting results. We will soon be expanding the solution to our greenhouses and sites to further compound the yield optimization benefits across the organization.
Key features of our Greenhouse Management, Monitoring & Yield solution:
- Environmental Monitoring - Environmental factors such as temperature, relative humidity, and light intensity have a profound effect on the growth of greenhouse crops, for optimal control and growth.
- Alerts and Notifications - Environmental control failures can have disastrous effects on crops, particularly if they occur at sensitive stages of crop development. It is therefore critical to receive notifications as soon as they occur in order to successfully take action.
- Real-time Insights - Quickly visualize KPIs across all of your greenhouse rooms, greenhouses and locations – wherever they are – in one dashboard.
- Yield Forecasting - Build models to forecast yield by combining historical monitoring data with actual crop yields in our machine learning workbench.
- Event Management - Control and monitor events directly – either automatically or manually control in-greenhouse actuators for lighting, CO₂, nutrient and irrigation delivery, etc.
- Energy Efficiency - Manage your energy use intelligently throughout the growing cycle to ensure that you maximise energy efficiency.
Real business outcomes driven by our Greenhouse Management, Monitoring & Yield solution:
- Greater predictability - Being able to better predict your crop yield and overall performance, means you can manage your business with more confidence. Reducing the uncertainty that is always present in farming, allows you to make better decisions with less risk.
- Lower cost of maintenance - Real time insights, alerts and notifications, together with forecasting, enables you to get a proper snapshot of how your business is performing and where your issues and risk lie, enabling to focus your resources more efficiently where actually needed.
- Reduce energy consumption - Energy is a high cost in most operations, and being able to reduce that cost, has a direct impact to the bottom line. Continues optimization of your energy consumption, means you can easily identify energy waste, which was never possible before, and operate with with more confidence.
- Reduced waste - With better real time visibility and predictability, you reduce the chances of issues not being identified, that may have irrecoverable consequences, like lost of crop.
- Increased yields - Real time visibility and predictability combined with smart algorithms and machine learning, and your custom business logic, means you can configure your solution to optimize conditions for maximum yield, and track your performance vs targets
- Increased margins - The combination of increased yield, reduced waste and energy consumption, lower cost of maintenance all contribute to your bottom line.
Get started with your own transformation today, fast and affordably.
Factory One's easy-to-use solution, complete with ready-to-deploy modules that can improve every aspect of your manufacturing operations, will give you all the abilities you need, plus much more, in weeks with no hidden-costs.
Speak to us today to get started.