How to start with predictive maintenance in manufacturing
Blog

So you’ve done your homework, you know what asset you want to use Predictive Maintenance (PdM) for, and have put together a business case for it - how do you get started with it?
What we will say at the outset is that Predictive Maintenance solutions should be manageable, not cost the earth, nor risk disrupting your operations. If this is the scope of the project that someone has come to you with, then run far, fast.
The key to the successful deployment of Predictive Maintenance is to start small. If you’ve identified the correct assets that it should be deployed for, i.e. that their business-critical and have multiple variables that affect their operation which cannot all be measured from a single sensor, then by definition the risk of something going wrong and disrupting your operations is significant. You’ll also know that, for it to be truly effective, it needs Data Science and Machine Learning, as well as time to build a large enough set of historical data to get things right – something you’re only going to be able to get after something is up and running to collect and process the data coming from it.
With that out the way, this is how we think Predictive Maintenance should be approached:
- Understand the way you currently maintain the asset and its current performance: discover where it’s commonly failing or which parts it’s needing changing frequently, what the current maintenance schedule is (i.e. when is there planned downtime), and discover what its current productivity is. What you’re looking to do here is collect enough data to get a baseline calculation of performance and understand points of failure so that you can collect the appropriate real-time data.
- Identify and deploy the correct IoT sensors and meters, plus integrate existing systems: what you’re looking to do is to establish real-time, accurate data streams into your IoT platform so that you can utilize data science and machine learning. It’s likely that you’ll need fit new sensors to old machinery, (which may need a specialist, depending on the machinery) and integrate existing systems (e.g. SCADA), so it might be best to seek some advice first.
- Build the Data Warehouse and programme the IoT platform: with all the sensors in place, you need to build the data warehouse where it will be stored (in the Cloud) and then tune your IoT platform so that it can process the information and visualize it. It’s at this stage that you should develop asset health scores and be able to visualize it – a big step!
- Data Science & Machine Learning: with the solution up and running, getting accurate real-time data streams, and providing a dashboard of readings, you can get started with building your machine learning algorithms that are going to predict failure. This might sound complicated, but some platforms (like ours!) have a drag-and-drop, codeless interface (Rayven’s Machine Learning Engine) which make it possible to build yourself.
- Simulate (or measure real) failures and deploy: once created, good IoT platforms (like ours!) can then allow you to test the algorithm in a simulator using different variables to track its efficacy in predicting failure. This presents you with the opportunity to finetune it before then deploying it into your real operations. There is likely to still be failures over this period as new scenarios occur, but these are all things that the machine learning algorithm will be learning from to help prevent in the future by adjusting failure thresholds.
- Optimize: as you collect more data over time, with Machine Learning, you can start to learn more about your asset’s performance, spots deeper trends in the data, and then further tune it so that you’re not only predicting failure, but also finding new, more effective ways of operating the asset or conducting maintenance. You’ll also be able to optimize your existing maintenance schedules and better organize maintenance crews to be more efficient.
- Scale: once you’ve a proven Predictive Maintenance model that’s demonstrating a clear bottom line benefit to your organization, then it’s time to scale the solution. If it’s on one truck, scale it to the fleet, one production line, move it to all others in different facilities. This is the stage where you compound the benefits and capitalize on the upfront investments that have been made in Data Science and Machine Learning. This will further increase the ROI of your project and open new opportunities for IoT technology deployment across your organization..
Factory One's approach to Predictive Maintenance (and all IoT projects) is to deploy small-sale preconfigured IoT solutions fast (and affordably), utilizing experts with in depth industry knowledge and experience in the field (as well as data science) who can then finetune it to your operations. Once you start collecting the right data and the machine learning algorithm is improving itself, you can judge the business impact and then scale..
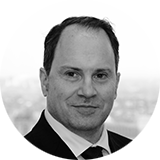
Dr Bernard Kornfeld
Chief Scientist
LinkedIn
Get started with your own transformation today, fast and affordably.
Factory One's easy-to-use solution, complete with ready-to-deploy modules that can improve every aspect of your manufacturing operations, will give you all the abilities you need, plus much more, in weeks with no hidden-costs.
Speak to us today to get started.