Why you should establish real-time OEE metrics
Blog

Overall Equipment Effectiveness (OEE) is a critically important measure for manufacturers, but measuring OEE accurately, consistently and at any given moment can be incredibly difficult for manufacturers.
Textbook vs. real-time OEE measurement
OEE provides managers with an overall measure of asset utilization and enables them to identify where major issues are, enabling them to focus improvement activities so that you can improve the bottom-line.
Whilst there’s a best practice technique for measuring it, every organization has a different approach and because every manufacturing plant runs in its own way, there are always variations. For example:
- What’s your access to data? Some tools have accessible PLC or SCADA output with downtime reasons, others have closed PLCs or none, so need external sensors.
- Is a scheduled break a preventable loss? Some say ‘no’, but staff might be able to be rotated through breaks to keep the line running.
- Some data is only accessible through manual extractions or cannot be connected to networks, meaning that you only get data once its use is already reduced.
- How are they coded? Every business has a different set of reason codes, and these may well need to be changed over time.
What’s common to all manufacturers is that you need to know what your baseline OEE calculation is before you can monitor it – even this can be a difficult.
To calculate OEE accurately, you need a system that can cater for all of your individual variations, as well as be able to adjust to changing conditions – not another company that exists only in a text book. The questions is how?
The six measures of OEE that go in to measuring availability, performance and quality:
Equipment failure or downtime
Planned stops for setups and adjustments
Idle time and minor stoppages
Speed or throughput losses
Process
defects
Yield
losses
*In walks Industrial IoT and integrated Industry 4.0 technology*
The extension and use of IoT and Industry 4.0 technology in the manufacturing space is part of the ongoing (and rapid) growth of industrial IoT or IIoT and broader digital transformation.
What it now enables you to do is to connect and retrofit existing machinery with sensors so that you can collect live, real-time data on performance from lots of different tools, systems and machines. Combined into an IoT platform, it can provide you with a live, real-time view of your OEE via data visualizations and dashboards.
This has a number of immediate advantages for manufacturers, both in the short and long-term:
- Get an accurate baseline OEE calculation – from this, you can then identify what under and over performance looks like and trigger alerts set at custom thresholds to trigger action.
- Make real-time production improvements – your production team can see how they’re performing against their daily targets, where the problems lie, and make make immediate Improvements.
- Prioritize future optimizations – managers can analyze their holistic line performance to tweak processes and inputs to plan for future optimizations.
Most importantly, knowing your real-time OEE provides you with complete transparency and a way of comparing performance at a machine, line, factory, region, national or international level. Through having access to this data, with industrial IoT, you can start to do much, much more.
Using Industry 4.0 technology to measure OEE is just the beginning
The potential uses of Industry 4.0 technology within the manufacturing industry are extensive.
Whilst establishing real-time OEE is a critical first step for most manufacturers, its effect isn’t felt much further than the manufacturing floor.
With the data collected from your production lines (and further afield), great data, AI + IoT platforms and providers versed in data science and machine learning, can use the data sets to achieve overarching business goals.
Other uses of Industry 4.0 technology within the manufacturing industry:
- Supply chain management: more efficiently manage your supply chain and reduce costs.
- Predictive and self-healing maintenance: know when a machine is underperforming or going to break, and fix it at scheduled stoppages before it causes a problem.
- Management modelling/Digital Twins: model new processes, products and improvements digitally; understand the effect that they’ll have and optimize them before you deploy them, saving money, time and resources.
- Efficiency/resource utilization: understand electricity, cooling/heating, water (etc.) usage trends, how they can be better used, and reduce costs.
- Improved production: fine-tune machines based on intelligence, reducing errors, duds and waste.
- Process improvement: see how new production processes, shift schedules or timings can improve productivity.
The list above is just the beginning. Fundamentally, Industrial IoT and Industry 4.0 technology is designed for you to understand your operations like never before, identify the optimizations you need to make to reach your business goals, and predict the future so that you can better handle maintenance, asset allocation, and production.
Truly, there is an almost limitless number of possible applications for the technology in the manufacturing sector, so the difficulty often comes with knowing what’s going to make the biggest difference fastest, how to start and who to work with.
Our advice would be to start small; pick a single measure and one production line, deploy quickly and test, see the results and measure the business impact, then scale - you do not need to spend hundreds of thousands of dollars straightaway, in fact, we’d actively encourage you not to.
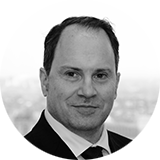
Dr Bernard Kornfeld
Chief Scientist
LinkedIn
Get started with your own transformation today, fast and affordably.
Factory One's easy-to-use solution, complete with ready-to-deploy modules that can improve every aspect of your manufacturing operations, will give you all the abilities you need, plus much more, in weeks with no hidden-costs.
Speak to us today to get started.